In the face of tough competition in today's market, it is becoming increasingly difficult for companies to set high prices for their products. Thus, there is a need for strict control of the cost of purchased raw materials and materials in order to plan production activities as efficiently as possible. With proper management, an enterprise can set markups on products sold, which in total sales will bring sufficient profit not only to cover all costs, but also to generate net profit.
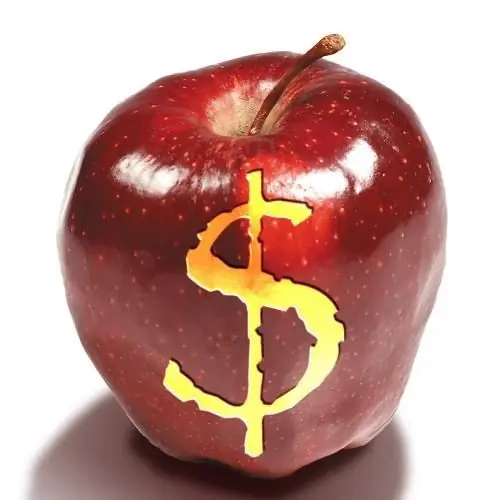
Instructions
Step 1
Several types of costs are involved in the formation of the value of the cost of production, the inclusion of which in the final price of the goods will allow setting such markups so that the enterprise can receive a net profit from sales. These are payments to suppliers, customs duties, interest to intermediaries for the purchase of materials, delivery of materials and other costs associated with the acquisition of the original goods and production.
Step 2
The costs of producing goods also include: payment for labor resources (wages), natural resources (water, land) and the cost of selling goods (advertising). The prime cost is formed for the reporting period, for which all of the above types of costs are taken. The objects of calculation are both individual types (categories) of goods and all products. To calculate the cost of finished products, the following methods are used: standard, process-by-process, by-pass and order-by-order.
Step 3
The normative method of calculation involves the following actions: calculating the cost price for each product, accounting for changes in existing standards throughout the reporting period, accounting for all costs with division into standard and deviated from the norm, setting the cause of deviation from the norm, calculating the total cost of products by summing the listed values. The standard set of costs is adopted individually at each enterprise and may change under the influence of various factors (for example, changes in prices for materials or equipment modification).
Step 4
The process-by-process method of calculating the cost price is used in enterprises that are characterized by mass production of one or two types of goods, the absence of complex technological processes. This method takes into account the costs of the entire consignment at once. For the convenience of counting, all production is divided into processes, hence the name.
Step 5
With the alternate calculation method, the production process is divided into stages, during which intermediate products (semi-finished products) are returned. These stages are called redistributions. Costs are calculated for each redistribution.
Step 6
The order-by-order calculation method is applied when posting costs for each individual order. The cost price of the products specified in the order is calculated after its completion. The calculation also includes indirect costs arising as the ordered products are manufactured.