The bending machine, depending on the type, can work with metal sheets of different thicknesses. There are CNC models that simplify the production process.
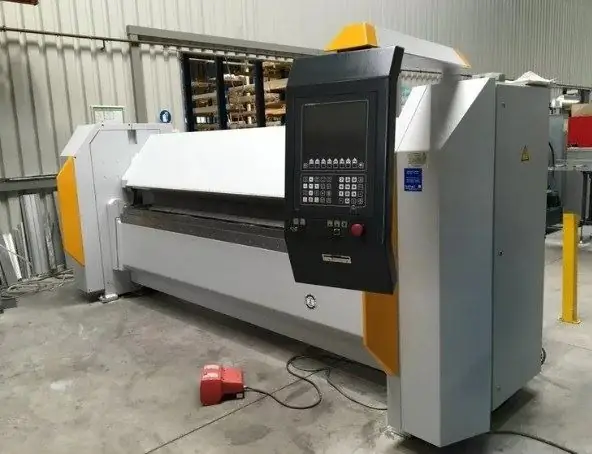
Bending machines are common equipment that is actively used both in large enterprises and in private workshops. Enterprises that make roofing elements and metal parts cannot do without them. The bending machine itself is complemented by special knives for cutting the material. The exact parameters of the product allow you to obtain the protractors used to set the desired angle.
Types of bending machines
There are several types of equipment:
- Manual. Inexpensive, often used in private workshops. The work of such machines can be performed by specialists with certain skills and strength.
- Mechanical. To obtain the desired fold, the flywheel is unwound. This type, like the previous one, is not used to perform a large amount of work.
- Hydraulic. They involve solving problems with the help of a liquid. Under pressure, it acts on a cylinder, which bends the sheet.
- Electromechanical. They have a motor that transmits force to the clamping bar. Suitable for bending thick materials.
How to choose
A bending machine with a reserve of characteristics is selected. This will allow you to quickly solve the assigned tasks, work with different material thicknesses. If you need a mobile device, focus on handheld models. They do not take up much space, but are relevant for thin sheets with a thickness of up to 2.5 mm. For enterprises, devices of a stationary type are suitable. They are more reliable and suitable for permanent use. They often have additional levers and clamps.
Before buying, check in which country the machine was made. Products from the USA, Poland, China and Germany are popular in Russia. The most budgetary ones are Russian and Chinese models. The most expensive are from Western European countries.
Bending machines of the new generation have software complexes (CNC). This makes it possible to design products on displays. Such equipment is more expensive, but allows several times to increase the productivity of work. Thanks to him:
- it is easy to reduce the number of people involved in production;
- you can create universal machines suitable for solving diverse tasks;
- the accuracy of parts manufacturing is increased;
- design costs are reduced.
Before buying a sheet bending machine, think about what strategy for the production of metal products you plan to use. Directly defining the product range. This will allow you to purchase a machine that has greater capabilities than you need now, but will save you money in the future.