In the face of increasing competition and a crisis in the economy, effective production management is becoming a major task. To solve it, it is necessary to develop an integrated approach based on the analysis of a number of factors.
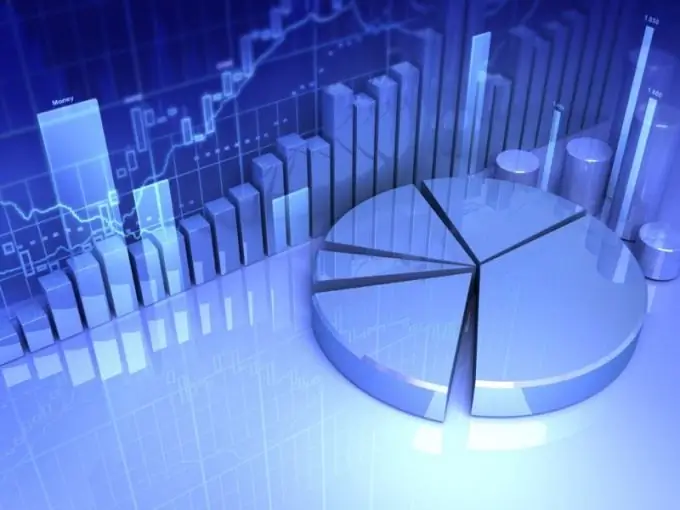
Criteria for evaluating production efficiency
Production efficiency is assessed based on a number of criteria. Quantified performance indicators are used more often in the analysis. Tracking their dynamics allows you to identify a decrease in production efficiency and take measures to resolve this problem.
One of the key analyzed criteria is profitability, which reflects the efficiency of using the resources of the enterprise. In general terms, profitability is the relationship between revenue (gross income) and total costs. It can be expressed through the indicators of net profit (the ratio of sales to profitability of sales), productivity (the ratio of the number of products sold to labor costs), as well as innovation (a factor that determines the competitiveness of production and the role of innovation in the production process).
The priority and specific weight of each of the criteria depends on the type of enterprise, its position in the market, staffing, etc. The task of enterprise management is to identify the key factors in the growth of production efficiency.
Most often, the solution to the problem of inefficient production comes down to three areas - the optimization of production costs, the introduction of innovations in production, and also a change in the management system.
Cost optimization
If, as a result of the analysis, it was revealed that the company occupies a low competitive position in terms of profitability and profitability of production, the primary task should be the development of measures to reduce costs. These may include, for example, steps to optimize raw material costs by seeking better commercial offers from suppliers or by changing ingredients and components of the manufacturing process.
Another option is to reduce fixed costs (eg rents, logistics costs) in the cost structure due to increased production. True, this can be done only if there are guaranteed sales markets for the products.
Finally, the third option is to optimize the headcount. For example, by outsourcing some of the services. This method was often used by companies during the financial and economic crisis, transferring accounting and legal functions to third-party contractors.
Modernization of production
In modern conditions, the use of innovations is one of the key factors of the company's competitiveness. After all, they allow you to reduce production costs and offer better quality goods.
Modernization can be carried out through the introduction of modern software or new, more efficient equipment. So, software can automate part of business processes, or improve internal communications between employees. In the context of the constant increase in the cost of energy resources, one of the significant factors in the growth of production efficiency may be the introduction of energy efficient saving technologies.
Change of the management system
Another popular method is the use of developed and well-proven management systems. Among them, the most widespread is the model of the Quality Management System (QMS) based on the requirements of ISO 9001. It is designed to improve the activities and increase the competitiveness of the organization.