The larger the batch size, the cheaper the transportation of the goods. At the same time, the cost of warehouse storage keeps from purchasing products in too large volumes. The more goods are brought in at a time, the higher it is, and the less efficiently the warehouse space is used. To solve this problem, it is necessary to correctly calculate the optimal batch size.
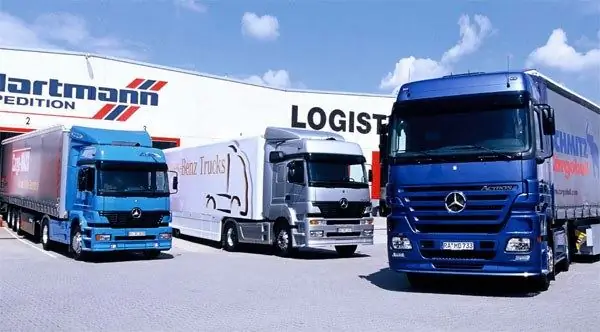
Instructions
Step 1
The calculation of the optimal level of stock allows you to determine the size of the batch, at which the total costs of storage and delivery are minimal.
Step 2
To calculate the required quantity of goods in one batch, you will need to determine three indicators: the total cost of servicing the order, the storage cost per unit of production, and the total consumption for the period.
Step 3
The costs of servicing an order are made up of such indicators as: preparation and maintenance of contracts, transportation, document flow and telephone conversations and the salary of an employee of the supply department.
Step 4
Data on salary, negotiation and workflow are taken for the billing period and divided by the number of units of goods received at the warehouse during this time.
Step 5
Shipping costs are also calculated per item. Summarize the obtained indicators and designate them C0.
Step 6
The next indicator that you will need for calculations is the warehouse costs per unit of production. To determine it, calculate how much it costs you to maintain the warehouse every month. This data includes rent or property taxes if you own the warehouse, warehouse staff salaries, and utilities.
Step 7
Calculate the average warehouse turnover per month in basic units (kilograms or pieces). Dividing the costs of maintaining a warehouse by the amount of turnover, you will find out how much it costs to store a unit of goods for a month. Designate this indicator H.
Step 8
The last indicator is the volume of consumption for the period. It is just the sales or production volume for the reporting period in base units. Label it as Q.
Step 9
Now plug the three obtained indicators into the formula known as the Wilson formula.
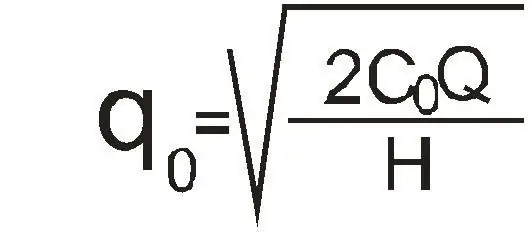
Step 10
The result q is the lot size at which the total costs will be minimal. Do not forget to round it depending on the multiplicity of packaging. So, if as a result you received the optimal batch size of 3608 pieces, and the ordered products are delivered in a package multiple of 20, round up the amount received to 3600 pieces.