Lean manufacturing allows you to optimize all business processes in the enterprise. It is aimed at eliminating costs, launching a continuous production process, targeting the end consumer.
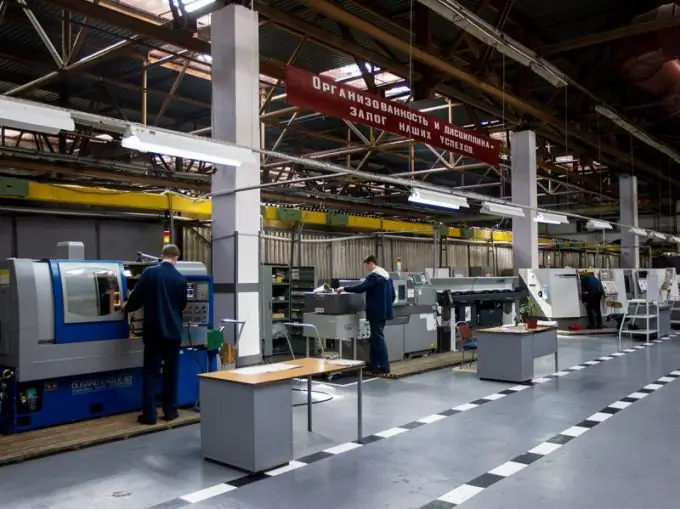
Lean principles are often used in enterprises to reduce costs. With their help, it becomes possible to reduce the number of actions that are not able to add consumer value to the production process.
Lean manufacturing refers to a special management scheme for a company. Its main idea is to strive to eliminate any kind of costs, to include each employee in the optimization procedure. Such a scheme is completely directed towards the consumer.
History
The founder of the concept is Taiichi Ohno, who developed the basic principles. He has worked for Toyota Motor Co since 1943. In 1945, Japan lost the war, in order to survive in a recession, a new approach to resolving issues was needed. In those years, America was the undisputed leader in the automotive industry. For years it has been cutting costs by increasing mass production. This style quickly became applicable in all areas.
The President of Toyota Motor Co said that it is necessary to catch up with America in three years. If this is not done, then the auto industry in Japan simply will not survive. Therefore, all efforts were spent on developing their own production system, which was different from the traditional Japanese mass production system. At the same time, the goals were achieved not by expanding production areas, but by producing cars in small batches according to a new scheme.
The key factor is reliance on the human factor and the creation of an atmosphere of mutual assistance. The new principles introduced were applied not only to employees, but also to customers and suppliers. Over the next 15 years, Japan experienced unusually rapid economic growth.
Features and principles
The main point is the assessment of the value of the manufactured product for a specific consumer. A situation is created in which there is a continuous elimination of losses. This makes it possible to remove actions that consume resources, but do not form values. Taiichi Ohno identified several types of losses:
- due to overproduction;
- waiting time;
- unnecessary transportation;
- unnecessary processing steps;
- formation of excess stocks;
- unnecessary movement of objects;
- the occurrence of defective products.
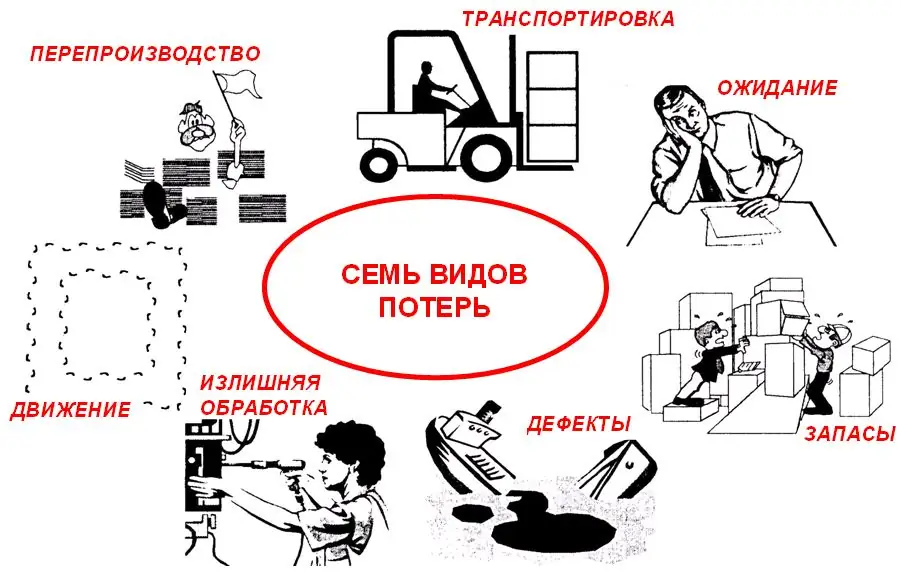
Refers to the types of losses and uneven performance of the operation. This happens, for example, with an intermittent work schedule of an enterprise due to fluctuations in demand in the consumer market.
To implement lean manufacturing, it is necessary not only to work out losses, but also to implement the basic principles. The first assumes: you need to determine what creates the value of the product from the point of view of the consumer. Sometimes a large amount of manipulation is performed at an enterprise, which turns out to be unimportant to a potential client. This approach will allow you to determine which processes are focused on providing value and which are not.
The second principle is aimed at identifying key points in the entire production chain and eliminating waste. For this, all actions are described in detail from the moment the order is received, to the transfer of the product directly to the buyer. This allows you to identify what is needed to optimize work and stimulate production.
The third principle involves restructuring activities so that they represent a workflow. This aspect assumes that all actions must be performed so that there is no downtime between them. Sometimes this aspect requires the introduction of new technologies. Then all processes consist of actions that have a positive effect on the product itself.
The fourth principle is the need to perform actions that are necessary for the consumer himself. The organization should only produce products to the extent that it will be sufficient.
The fifth principle is the need for continuous improvement by reducing unnecessary actions. Implementing the system will not work if the principles are used only occasionally. If you decide to start implementing the system, you need to do this constantly.
Lean tools
They make it easier to use lean principles. The tools are applied individually and combined. These include:
- Organization of the right space. Comprehension of problems occurs, detection of various deviations.
- Problem reporting system. A special signal is given. It is allowed to stop production to prevent massive occurrence of defects.
- Stream alignment without interruptions and buffer accumulation. This tool makes it possible to eliminate various types of losses ranging from surplus stocks.
- The most important thing happens not in offices, but in production sites. The involvement of the management reduces the reaction time when any problems arise. Discipline and first-hand information are being strengthened.
- The overall efficiency of the equipment is always checked. This tool tracks three categories of equipment loss: availability, productivity, and quality.
There are other lean manufacturing tools, all of which are aimed at the transparency of management processes, reducing the cost of product quality and increasing the involvement of employees in the production process.
Features of Lean Manufacturing Methods
The concept is simple to understand, but hard to make it work in practice. Often times, implementing the principles requires a change in the entire culture of the company. This may require not only time, but also money. The concept is focused on the maximum consideration of the interests of customers and consumers. The high organization of all processes allows you to avoid unnecessary costs and compete in the modern market.
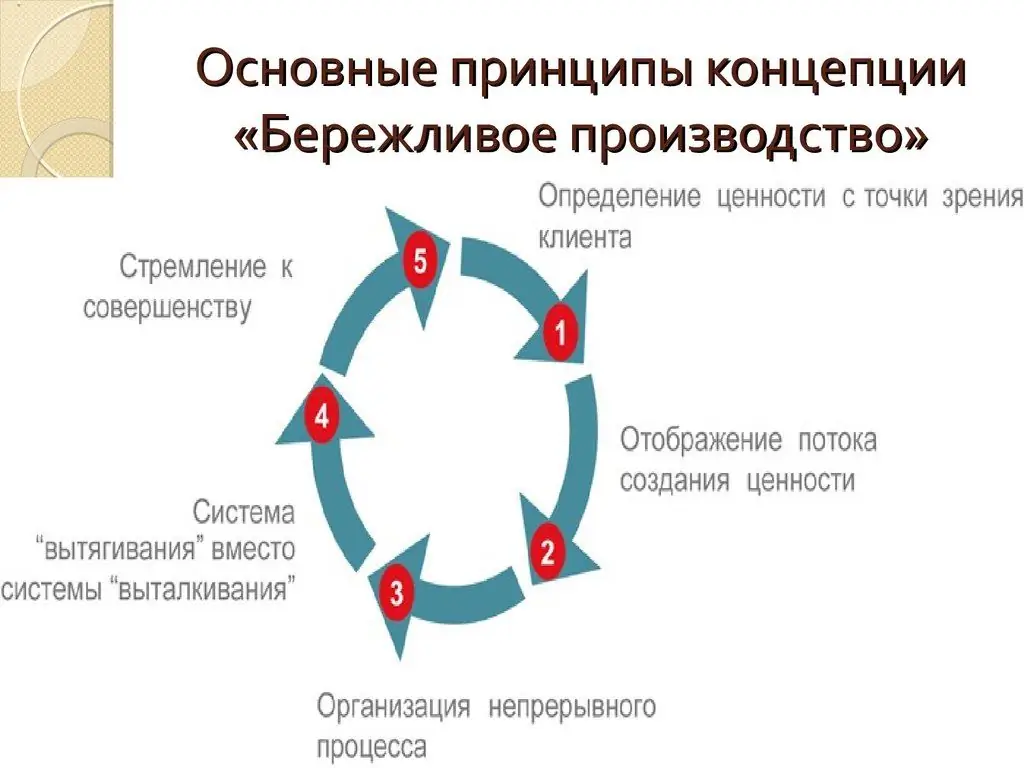
World experience shows that the implementation of the described principles:
- increases labor productivity by 35-70%;
- reduces the production cycle time by 25-90%;
- reduces the possibility of marriage by 59-98%;
- increases product quality by 40%.
Lean principles can be applied in a variety of areas. These aspects are especially relevant in production, logistics, banking, trade, information technology, construction, and medical services.
The implementation of the principles takes place in three stages. First comes the study of demand. For this, calculations of pitch, takt time and other special technologies are used. In the second stage, the continuity of the value stream is achieved. Certain measures are being taken that make it possible to provide consumers with products in a timely manner and in the right quantities. At the third stage, smoothing occurs when there is a balanced distribution of volumes and work performed.
Implementation will be successful if the full range of tools and resources are used in the process, and a training plan and employee qualifications have been approved. The latter is important, since when employed in a company, people are usually invited who have different knowledge, skills and experience. You can learn from experience both using special training programs and by observing colleagues.
In addition, Lean Manufacturing involves the development of creativity in employees. This approach allows you to go beyond a specific enterprise to work effectively in any direction. All employees must be able to find different solutions to the same situation.