Production capacity is an indicator of the maximum possible output of products, the provision of services or the performance of work in accordance with the established nomenclature and using all available resources. This value is measured in physical terms (tons, pieces, kilometers, etc.) and depends on the capabilities of the enterprise's equipment.
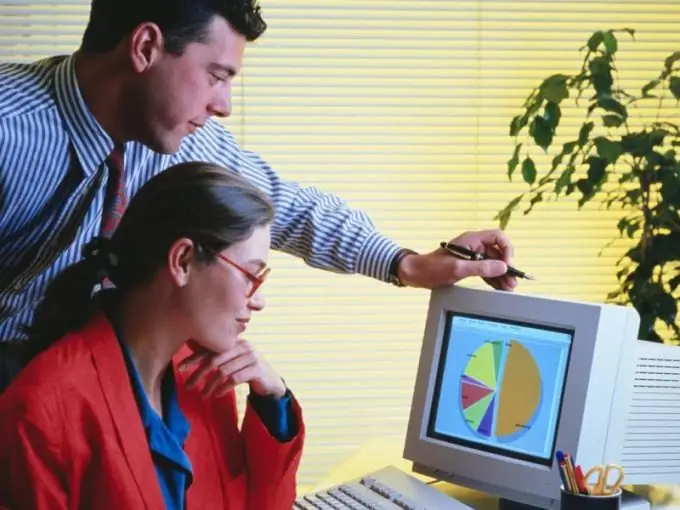
Instructions
Step 1
Specify the production and technical structure of the site and workshops. Distribute work by piece of equipment. Analyze the manufacturing processes that take place in the course of activities and release of products.
Step 2
Determine the labor intensity of the site according to the current regulations, taking into account the progressive use of the equipment. After that, determine the throughput of the equipment, dividing it into interchangeable groups. To do this, you first need to calculate the effective annual fund of equipment time. It is equal to the product of the number of working days per year by the length of the working day and the number of shifts per day of equipment operation.
Step 3
After that, correct the obtained value by one minus the coefficient of planned loss of time, divided by 100. Multiply the resulting annual fund by the number of pieces of equipment and divide by the time required to manufacture products on this equipment.
Step 4
Analyze the obtained value and select the leading group that will be used when calculating the capacity of the site. Identify bottlenecks that are associated with equipment that has much lower throughput than the lead group. Develop measures for their elimination and for the use of underloaded equipment.
Step 5
Calculate the production capacity of the workshop, taking into account the production capacity of the site. Thus, by increasing the objects, you will reach the enterprise as a whole. After determining the production capacity, it is necessary to analyze the state of the enterprise and adjust its activities to changes in demand. To reflect the efficiency of using equipment, it is necessary to divide the actual or planned volume of production by production capacity and compare the resulting value with other indicators of the reporting periods.