Dry building mixes are dosed sets of ingredients required for various construction and renovation work. The most common of them are dry concrete and mortar. These products will always be in demand, since no construction is complete without their use.
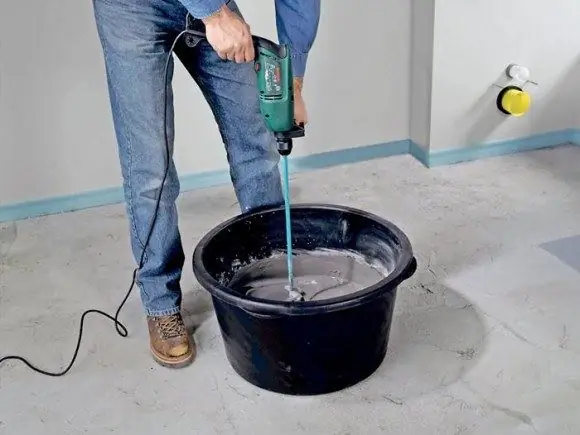
Instructions
Step 1
Start by planning your production organization. Collect detailed information on the types of dry building mixtures, technologies for their preparation, the required equipment. Study the existing market for these products in the region and the prices at which they are sold.
Step 2
Decide what kind of building mixtures you will produce, and find out what equipment is required, its performance, cost, the possibility of leasing. So, for a small production of dry modified building mixtures (plaster, tile adhesives, putties), a set of equipment will be required, consisting of a loading unit, a screw feeder, a vibration dryer, a sieve, an additive dispenser, a mixer, an elevator and an automation kit.
Step 3
Calculate the required floor space based on the performance and size of the equipment. Check the storage conditions for raw materials and ready-made dry mixes. Choose a room taking into account these conditions, find out the cost of renting it.
Step 4
Find out how much electricity this equipment will consume. Calculate your energy costs. Check the prices of raw materials for production from various suppliers in the region. Target future consumers of the product. Decide on the delivery of raw materials and ready-made mixtures - by your own or hired transport.
Step 5
Calculate how many people and what specialty you need to work in a small production. At a minimum, you will need a technologist who will compose mixtures formulations, an installation operator, a loader who knows how to operate a forklift. Decide how you will keep your accounting - yourself or hire an accountant.
Step 6
Based on the collected data, draw up a business plan with a budget for income and expenses. Calculate the estimated initial costs (start-up capital) and costs of the main production and sales of products. Be sure to factor in advertising costs. A business plan can be ordered from specialists, they will collect all the information themselves and perform the necessary calculations.
Step 7
Find out the possibility of obtaining a bank loan to start a business. Decide on the type of business - LLC or individual entrepreneur. Prepare the necessary documents and register the company.
Step 8
Enter into all the necessary contracts: for the lease of premises, for the supply of equipment and raw materials, for transport services, etc. Purchase the selected equipment, arrange for its delivery, installation and configuration. Purchase raw materials and supplies for production.
Step 9
Hire workers - through advertisements, through recruitment agencies or by applying to the employment service. Purchase a computer, printer and fax. Install an accounting software.
Step 10
Be sure to engage in advertising products, this is very important at the initial stage of the work of even a small enterprise. Contact advertising agencies, order advertising on TV and radio. Submit ads to newspapers, including those that are distributed free of charge. You can order the creation and promotion of the company's website on the Internet.
Step 11
Send commercial offers, price lists by fax to potential customers, offer products through telephone conversations. So you will quickly build up a customer base for dry building mixes of your production. If your budget allows, hire a qualified sales person.
Step 12
Pay attention to actual production costs by looking for cost savings and efficiency gains. This will allow you to quickly recoup the initial investment and then use the profit to develop and expand the production of dry building mixtures.